Олег Ведмеденко
БУДНИ ИСПЫТАТЕЛЕЙ ЖРД

|
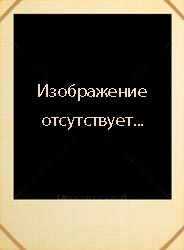
Олег
Ведмеденко |
|
Выпускник ФТФ ДГУ 1960 г.
В предыдущей книге «Профессия с грифом «секретно» (в статье «Воспоминания испытателя») я пытался охватить основные (узловые) моменты в жизни испытателя.
Но наряду с ними были обычные будни, иногда и курьезные.
В связи с отсутствием нормативной документации на проведение испытаний (технологический процесс, карта подготовки и проведения испытаний – в дальнейшем предъявительская на испытание и т.д.) было принято решение (после первого взрыва на стенде № 1) срочно её издать.
Начальнику стенда Панарину И.И. поручено написать технологический процесс (ТП) подготовки и проведения испытаний рулевых ЖРД. Так как у него в подчинении был я «молодой специалист», то часть работы была поручена и мне. Составить список инструмента и крепежных деталей, применяемых при каждой операции. Я в течение нескольких дней (практически участвуя в каждой операции) составил такой перечень и передал его Панарину И.И. Прошло примерно две недели и вдруг начальник приглашает меня к себе и, вывернув при мне все свои карманы (место хранения черновиков ТП), заявил, что я или не давал ему перечня или «возможно» он его куда-то «засунул». Пришлось, ругаясь про себя, делать повторный перечень. Наученный горьким опытом, я оставил себе второй экземпляр (под копирку), отдал перечень начальнику и успокоился. Но через некоторое время все повторилось. Отдавая «запасной» перечень Ивану Ивановичу заявил: «Это третий экземпляр! И больше я делать не буду!». Какова была моя радость, когда где-то месяца через два ТП был выпущен. Это был первый ТП по испытаниям двигателя ЖРД.
Двигатели приходили для испытаний собранными на так называемом технологическом кольце (имитатор части ракеты) с вертикальным расположением, т.е. сопла камер сгорания были направлены вниз (для удобства транспортировки в спецконтейнере). Возле лаборатории они разгружались на спецтележку и транспортировались на склад или на стенд. Стенд же имел расположение переходной рамы станка горизонтальное. Для установки двигателя на стенд его приходилось «переворачивать», т.е. поворачивать на 900 вдоль оси. «Средством» переворота и установки двигателя на стенд был башенный кран грузоподъемностью одна тонна, (камера ЖРД весила около 900 кг). И вот манипулируя подъемом троса и стрелы необходимо было выполнить операцию «переворачивания». При этом наступал момент (при нечеткой манипуляции кнопками управления – это делал рабочий-механик), когда камера как бы зависала в воздухе, а затем «опрокидывалась» занимая горизонтальное положение. Это была рискованная операция. Поэтому технологическому отделу завода п/я 186 было поручено разработать, а цехам завода изготовить специальный кантователь. Конструктора при разработке «хорошо» поработали, и получилась еще та «бандура». Под неё пришлось делать специальный фундамент. Для плавного переворота на кантователе был установлен редуктор с электродвигателем. Двигатель был маломощным и вышел из строя. Заменить было нечем. Хозяйство ведь плановое! Поэтому была произведена доработка для ручного «кручения» редуктора. Так как передача у редуктора была «медленная», то приходилось крутить ручку очень долго. И ребята «соревновались» в том, что сделает больше оборотов. А так как они были в основном молодые, только демобилизованные из армии, то считалось: «Кто больше выкрутит, у того родится мальчик».
Все операции по подготовке стенда, двигателя, а также проведения самого испытания, проводились под контролем работников бюро технического контроля и представителей заказчика (военпредов). А так как они в основном пришли из армии (летчики, артиллеристы, моряки), то приходилось для них еще и проводить «ликбез» по системам стенда и изделий. Но среди них попадались и такие, которым никакой «ликбез» не помогал. Они считали себя «пупом» земли. Ведь они заказчики! Так однажды капитан Зиноватный подошел ко мне и, показывая капли воды на своей форменной фуражке (первое время военпреды ходили в форме), заявил: «Все! Испытания не будет, у тебя стенд течет». Долго пришлось ему объяснять, что для проверки включалась система водяного пожаротушения и эти «капли» остатки воды.
Одним из показательных эпизодов срочности и одновременности отработки и поставки двигателей в «товар» (для сборки ракет) был и такой случай.
При разборке двигателей после испытаний в трубопроводах последних обнаруживались новенькие плоские шайбы. Была создана комиссия во главе с главным инженером завода Макаровым А.М. (позже директор ЮМЗ). Комиссия предположила, что наши рабочие монтируя двигатель на стенде, роняли туда шайбы. Обыскали тумбочки у рабочих, но ни одной шайбы не нашли. А все оказалось просто. При промывке отсечных пироклапанов двигателя зазор регулировался (для получения определенного расхода жидкости) установкой на пироболт шайб, которые затем должны были заменяться специальными проставками. В спешке эту операцию забыли выполнить и вот результат! Шайбы после срабатывания пироклапана рассыпались и давлением продувки после останова разносились по трубопроводам.
При отработке двигателей производилось большое количество измерений давлений, температур, расходов жидкостей, пульсаций и вибраций. При этом качество замеров обусловливалось качеством подготовки и типами приборов (датчиков), применяемых для измерений.
В процессе отработки они изменялись как по параметрам, так и по методам дешифровки после испытаний. В начале (шестидесятые годы) основными приборами для точного измерения давления были манометры. В процессе испытания менялись режимы работы двигателя, да и сам процесс горения топлива в камерах сгорания был пульсирующим. Эти процессы необходимо было фиксировать как можно чаще. Но так как для фотографирования манометров применялись авиационные фотоаппараты, то чаще чем один кадр в секунду было делать нельзя. Да и запас фотопленки в аппарате не бесконечен. Для длительных испытаний применялось несколько аппаратов, да еще и с дубляжом. Затем пленка проявлялась, и необходимо её было расшифровать (т.е. снять все параметры по времени на секундомере, который фотографировался одновременно с манометрами). Это тяжелый монотонный труд через специальную лупу. Я его познал, когда был на преддипломной практике. Надо было зарабатывать на жизнь! Но так как процесс пульсирующий, то необходимо для картинки иметь непрерывную запись. Это осуществлялось с помощью датчиков давления (ДДИ – датчик давления индукционный) с записью на осциллограмму. Перед установкой на двигатель датчики тарировались на специальном гидропрессе с записью на осциллограмму. По результатам тарировки строились графики, по ним оценивались результаты испытаний.
Начав с манометров и датчиков ДДИ мы к концу шестидесятых пришли к замеру давлений датчиками ДДП (датчик давления потенционометрический) и ДДВ (датчик давления вибрационный). Их показания записывались на магнитную ленту (для дубляжа на осциллограф) и на ЭВМ.
Первое время мы не очень доверяли ЭВМ. Эти показания использовали как предварительные, для экспресс-анализов. Но настойчивая работа по применению ЭВМ Ботвинкиным В.М. принесла свой результат. И, в конце концов, измерения и обработка результатов испытаний на ЭВМ в автоматическом режиме стали основными.
Расчетчики, выпускавшие отчетную документацию по результатам испытаний, стали заниматься в основном анализом проведенных испытаний, а не рутинной работой по «съему» данных с фотопленок и подсчетов «пичков» на осциллограммах, выдаваемых датчиками расходов.
Нам, испытателям, приходилось заниматься не только подготовкой и проведением испытаний, но и одновременно курировать изготовление материальной части стендов на ЮМЗ, вести профилактический ремонт оборудования стендов, замену агрегатов ПГС (отсечные клапаны, вентили, редукторы и т.д.).
В начале 80-х годов агрегаты ПГС стали унифицированными. Их изготавливали на одном из заводов отрасли и поставляли по нашим заявкам. Для их ремонта и подготовки к установке на стендах было создано специальное подразделение. И возглавил его бывший инженер-испытатель Редько М.И.. Ему, как говорится, и «карты» в руки. Так назывались паспорта на агрегаты ПГС.
Одновременно с подготовкой и проведением испытаний мы, испытатели, принимали активное участие в выпуске технологической и конструкторской документации, а также отчетов по проведенным испытаниям. Мы знали её изнутри, т.е. прощупали руками и умом двигатель и стенд.
На всех ответственных участках подготовки и проведения испытаний в основном были выпускники физтеха.
 
|