Глава VI
УСТРОЙСТВО РАКЕТНОГО ДВИГАТЕЛЯ
НА ЖИДКОМ ТОПЛИВЕ
1. Предварительные замечания
Судя по тем данным, которые до сих пор были опубликованы в литературе, проблема конструирования ракет на жидком топливе нигде еще не получила реального воплощения, если не считать нескольких сделанных за границей попыток пуска опытных аппаратов, попыток, которым часто предшествовала пышная реклама, но которые неизменно сопровождались авариями и взрывами. Почти во всех случаях это было вызвано неустойчивой работой двигателя.
В этой главе мы излагаем те основы, которые на наш взгляд должны быть приняты при конструировании ракетного двигателя на жидком топливе, и рассматриваем различные формы выполнения его главнейших механизмов.
Наиболее важными вопросами в разработке двигателя являются: подача топлива в камеру сгорания, образование рабочей смеси в камере, зажигание рабочей смеси, защита двигателя от действия высокой температуры и выбор материалов для него. Эти основные вопросы мы сейчас и разберем.
2. Подача топлива в камеру сгорания
Задача состоит в создании избыточного давления для введения жидкого топлива в камеру, где происходит сгорание топлива под давлением. Разность этих давлений, так называемое давление подачи, идет на преодоление сопротивления движению топлива в трубопроводах и на впрыскивание этого топлива в камеру сгорания.
Ниже мы рассмотрим различные способы введения жидкого топлива в камеру сгорания, принимая давление в ней постоянным.
Жидкое топливо, как мы видели, обычно состоит из двух компонентов – окислителя и горючего, хранимых для безопасности в отдельных баках. Эти компоненты подаются по той же причине раздельно. Способы подачи того и другого в основном одинаковы, поэтому в дальнейшем мы будем рассматривать подачу одного из компонентов, называя его просто топливом.
Для подачи топлива из баков в камеру сгорания могут применяться следующие способы:
А. Непосредственное проталкивание топлива из бака в камеру сгорания с помощью сжатого газа. Здесь возможны два варианта. По первому (фиг. 52) сжатый газ 1 помещен над уровнем топлива 2 в баке 3. Начальное давление газа должно быть выбрано таким, чтобы по мере вытеснения топлива и опорожнения бака давление в нем все время оставалось большим, чем в камере сгорания. Для сохранения постоянства давления в камере сгорания может быть применен редукционный клапан 4. По второму варианту (фиг. 53) сжатый газ 1 помещается в отдельном баллоне 2, называемом аккумулятором давления. Газ поступает в бак 4 через редукционный клапан 3, служащий для поддержания давления в баке на постоянном уровне.
|
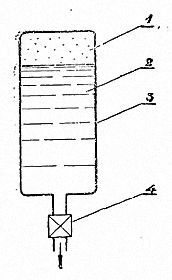
Фиг.52 |
|
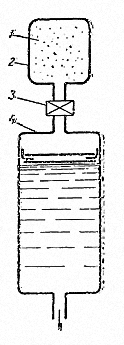
Фиг.53 |
|
Сравнивая эти два варианта, не трудно заметить, что помещение сжатого газа в одном баке с топливом нецелесообразно, так как высокое начальное давление газа обусловливает высокий вес бака. Второй вариант характеризуется постоянством давления подачи, простотой устройства и вытекающей отсюда надежностью действия, благодаря чему этот способ может найти применение в условиях лабораторно-исследовательской работы с ракетными двигателями, а также для маломощных ракетных аппаратов, предназначенных для полетов на сравнительно небольшие дистанции. Для мощных аппаратов этот способ неудобен вследствие тяжеловесности как. самих баков, так и аккумуляторов давления.
При подаче топлива сжатым газом желательно применять газы, неспособные вступать в реакцию с заключенным в баке топливом. Такими нейтральными газами являются: углекислота, азот и благородные газы. Применение воздуха, водорода и некоторых других газов может вызвать взрыв в трубопроводах и в баках, если допустить соприкосновение этих газов с тем компонентом, с которым они способны вступать в реакцию.
Следует также учитывать удельный вес газа, так как при тех высоких давлениях, которые имеют место в аккумуляторе давления, вес газа становится заметной величиной, как это видно из табл. 10, в которой указаны веса 1 м3 некоторых газов при давлении в 200 кг/см2 и при нормальной температуре.
Таблица 10
Газ |
Вес 1 м3
кг |
Газ |
Вес 1 м3
кг |
Водород |
18,0 |
Воздух |
259 |
Гелий |
35,6 |
Кислород |
286 |
Неон |
180 |
Аргон |
357 |
Азот |
250 |
Углекислота |
395 |
Из нейтральных газов наиболее подходящим является азот благодаря его доступности и не очень большому удельному весу. Углекислый газ представляет большое неудобство тем, что его критическая температура высока (+31°).
Использование водорода представляется очень заманчивым, так как он в 14 раз легче азота. Для подачи горючего водород можно использовать без опасений, для случая же подачи окислителя необходимо принять меры предосторожности. Одной из таких мер может служить отделение жидкого окислителя от газообразного водорода подвижной перегородкой, снабженной надежным уплотнением, как это показано на фиг. 53. При отсутствии такой перегородки в камеру сгорания в конце работы двигателя может попасть смесь окислителя с газообразным водородом, т. е. взрывчатая смесь, которая, воспламенившись, передаст огонь по трубопроводу в бак окислителя и вызовет взрыв. Подобное явление может произойти и при подаче горючего сжатым воздухом.
При подаче топлива с помощью аккумулятора давления сжатый газ, поступающий в топливный бак, вследствие своего расширения охлаждается, и тем сильнее, чем быстрее расходуется топливо. Если топливные компоненты или один из них являются сжиженными газами, то охлаждение .подающего газа усиливается. Это явление следует учитывать при определении потребного количества сжатого газа или степени его сжатия.
Если топливо целиком или частично состоит из сжиженных газов, то температура сжижения подающего газа при давлении подачи должна быть значительно ниже температуры сжиженных газов, составляющих топливо. В связи с этим применение, например азота, для подачи жидкого кислорода было бы нецелесообразно, так как температура сжижения азота лишь на 13° ниже температуры сжижения кислорода. Ясно, что при температуре жидкого кислорода упругость паров азота будет очень мала и потому для создания в баке нужного давления пришлось бы взять азота по весу значительно больше, чем для подачи жидкости при нормальной температуре. Жидкий кислород выгоднее подавать водородом, температура сжижения которого на 70° ниже, чем кислорода, или, еще лучше, нейтральным гелием.
|
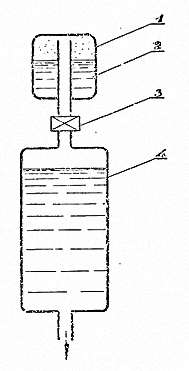
Фиг.54 |
|
Вариантом подачи топлива сжатым газом является способ, иллюстрируемый фиг. 54. В аккумуляторе 1 вместо сжатого газа помещен сжиженный газ 2, пары которого поступают в топливный бак 4 через редуктор давления 3. Объем аккумулятора при этом значительно сокращается. Для испарения сжиженного газа в аккумуляторе можно использовать теплоту, выделяемую самим двигателем, например, отводя для этого из камеры двигателя часть продуктов сгорания топлива. Можно также производить нагрев с помощью электрического тока.
Во всех случаях этот способ требует приспособлений для точного регулирования притока тепла к подающей жидкости.
Вместо сжиженного газа можно также использовать твердые и жидкие вещества, способные при химическом разложении выделять достаточное количество газов. Примером может служить обыкновенный бездымный порох. Однако получение длительного равномерного горения пороха затруднительно, и такая система подачи не поддается управлению.
Б. Подача топлива с помощью насосов. Подача топлива с помощью насоса имеет то преимущество, что разгружает топливные баки от внутреннего давления и тем самым позволяет уменьшить мертвый груз.
Мощность насоса, потребная для накачивания 1 кг топлива, равна
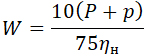
где P — давление в камере сгорания,
p — давление подачи (избыточное),
ηн — к. п. д. насоса.
Если P = 25 кг/см2, p= 25 кг/см2, ηн = 0,5, то мощность насоса на каждый килограмм качаемого в секунду топлива составит:
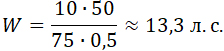
Так как расход топлива в ракетном двигателе исчисляется килограммами и даже десятками килограммов в секунду, то потребная мощность насоса будет порядка нескольких десятков или даже сотен лошадиных сил.
Насос можно приводить в действие с помощью независимого двигателя, но в этом случае механизм подачи оказывается громоздким и сложным. Значительно проще использование работы самого ракетного двигателя путем отвода из камеры сгорания части продуктов сгорания топлива для приведения в действие насоса.
Произведем примерный расчет такой системы подачи топлива для рассмотренного выше частного случая, для которого мы нашли, что потребная мощность насоса на каждый кг качаемого в секунду топлива составляет 13,3 л. с. Полагая, что к. п. д. промежуточного двигателя, связанного с насосом и приводимого в действие продуктами сгорания ракетного двигателя, равен 0,2, получаем, что затрата энергии на подачу 1 кг топлива эквивалентна мощности 13,3/0,2 = 66,5 л. с.
С другой стороны, если топливо имеет теплотворную способность в 1450 кал/кг (смесь азотной кислоты с керосином) и к. п. д. ракетного двигателя равен 0,5, то мощность этого двигателя при расходе топлива в 1 кг/сек, на основании формулы (16), будет равна:

Работа, расходуемая в секунду на нагнетание топлива, составляет:
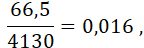
т. е. всего 1,6% от мощности ракетного двигателя.
Выгодность такого устройства несомненна, так как вспомогательный двигатель можно сделать достаточно легковесным. При более калорийном топливе относительный расход энергии на подачу топлива будет еще меньше.
Заслуживает также внимания применение так называемых взрывных насосов типа Хемфри-Оберта.
|
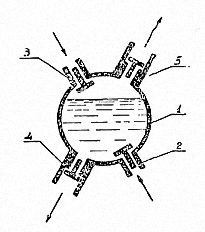
Фиг.55 |
|
Схематическое устройство такого насоса показано на фиг. 55. В камеру 1 насоса через питательный клапан 2 поступает из баков определенная порция одного из компонентов топлива, после чего этот клапан закрывается, а через клапан 3 в камеру впрыскивается небольшое количество другого компонента; например, если качается окислитель, то в камеру насоса впрыскивается горючее, образующее с парами окислителя взрывчатую смесь. При воспламенении этой смеси, например с помощью искры, в камере насоса происходит резкое повышение давления, действием которого топливо выталкивается через клапан 4 в камеру сгорания двигателя, после чего открывается выпускной клапан 5 и давление в камере насоса падает до атмосферного. Клапан 5, регулирующий поступление взрывчатой смеси, и клапан 5, служащий для выпуска газов из цилиндра насоса после выталкивания топлива, должны управляться специальным распределительным механизмом. Клапан 2 всасывающего трубопровода и клапан 4 напорного трубопровода могут действовать автоматически при изменении давления в камере насоса.
Недостатками взрывного насоса являются главным образом сложность распределительного устройства для клапанов, прерывистое действие, а следовательно, и непостоянство давления подачи и, наконец, опасность взрыва в случае прорыва газов из камеры сгорания через клапан 4 в камеру насоса. Соединение нескольких насосов, действующих попеременно, и включение во всасывающий и напорный трубопроводы газовых клапанов может до известной степени смягчить эти недостатки.
В. Другие способы подачи. Ниже мы вкратце остановимся на нескольких способах подачи топлива, которые хотя и менее рациональны, чем ранее рассмотренные, но не лишены интереса.
|

Фиг.56 |
|
К. Э. Циолковский, разбиравший в своих трудах несколько вариантов питания двигателя, предлагал отводить часть газов из камеры сгорания, используя их скоростной напор в специальном инжекторе для подачи топлива из баков в камеру сгорания. Этот способ невыгоден, так как к. п. д. инжекторов очень мал, и потому на подачу топлива пришлось бы затратить значительную часть мощности двигателя.
Для подачи сжиженных газов предлагалось использовать давление паров, образующихся при естественном испарении этих жидкостей или при их подогреве. Этот способ по существу ничем не отличается от рассмотренного выше (см. фиг. 54).
He лишено оригинальности предложение использовать реактивную силу для создания напора в топливном баке. Схематически это изображено на фиг. 56. Камера сгорания 3 укреплена на поршне 2, могущем перемещаться вдоль бака 5. Второй бак 6 отделен от бака 5 подвижным поршнем 1 со штоком 4. С началом работы двигателя действие реактивной силы на поршень 1 вызывает перетекание горючего из бака 6 в камеру сгорания, а окислитель из бака 5 проталкивается вследствие сближения поршней.
Расчет показывает, что при этом способе возможно осуществить лишь очень малое давление подачи, так как в противном случае нужно было бы иметь очень длинные баки для получения большого удельного давления поршня.
Следует упомянуть еще об использовании напора встречной струи воздуха для создания давления в баках. Этот способ осуществим при больших скоростях движения, притом в низких слоях атмосферы. Соединение этих обоих условий для полета ракетного аппарата очень редко будет иметь место.
Наконец, предлагалось использовать также силы инерции, возникающие при ускоренном движении ракеты. Получаемое при этом давление в баке имеет наибольшую величину у дна бака и будет тем больше, чем выше столб жидкости и чем больше ее удельный вес и ускорение ракеты. На практике это давление не превысит нескольких атмосфер и потому может быть рационально использовано лишь в сочетании с насосом, именно для подачи топлива из бака в цилиндр насоса.
Сопоставляя рассмотренные способы подачи топлива в камеру сгорания, мы видим, что для маломощных ракет, а также для экспериментальных исследований наиболее целесообразным является применение аккумулятора давления, который при достаточной простоте устройства гарантирует надежность действия двигателя.
Для мощных ракет, рассчитанных на длительную работу двигателя и большой радиус действия, аккумулятор давления является слишком тяжеловесным механизмом, и здесь нужный эффект может дать лишь применение насоса, причем наилучших результатов следует ожидать в случае использования газов самого двигателя для приведения насоса в действие.
3. Образование рабочей смеси
Качество рабочей смеси имеет чрезвычайно важное значение для ракетного двигателя. Чем лучше смешаны компоненты топлива, тем больше скорость горения и полнее сгорание. Чем лучше система смесеобразования, тем выше к. п. д. двигателя и тем меньше потребный объем камеры сгорания.
В ракетном двигателе задача удовлетворительного смешения компонентов топлива представляется особо трудной в связи с весьма большим секундным расходом топлива.
Здесь можно указать два основных способа образования рабочей смеси: смешение компонентов топлива вне камеры сгорания и смешение в самой камере. Возможна еще и комбинированная система смесеобразования, при которой в камеру сгорания вводится частично готовая топливная смесь и отдельно добавляется недостающий компонент.
С точки зрения получения совершенной рабочей смеси несомненные преимущества на стороне двигателя с предварительным смешением компонентов вне камеры сгорания. Схематически этот способ представлен на фиг. 57. Смесительная камера 4, которую можно назвать карбюратором, соединена трубопроводами 1 с топливными баками и сообщается с камерой сгорания 2 трубкой с помещенной в ней форсункой 3. При этом способе камера сгорания может иметь небольшой объем, так как топливо в нее будет поступать достаточно хорошо перемешанным.
Однако применение этого способа связано с очень большими трудностями. Дело в том, что готовые смеси жидких компонентов представляют собой, как правило, взрывчатые вещества исключительной силы. Таковы, например, смеси азотной кислоты или азотного тетроксида с углеводородами (панкластиты) или смеси жидкого кислорода с керосином, нефтью (оксиликвиты), употребляемые в военной технике и в подрывном деле. При тех давлениях, которые развиваются в камере сгорания, такие взрывчатые смеси легко детонируют.
Для правильной работы такого двигателя необходимо, чтобы скорость подачи жидкой смеси из карбюратора в камеру сгорания в точности равнялась скорости распространения реакции горения в топливной смеси.
Кроме того, необходимо, чтобы окислитель и горючее были способны взаимно растворяться без химического взаимодействия и оба существовать в жидком состоянии при температуре их смешения в карбюраторе. Если бы удалось получить жидкий раствор, скоростью горения которого можно было бы легко управлять, то задача была бы решена.
Подобные твердые смеси известны. Например, при растворении пироксилина в нитроглицерине получается так называемый нитроглицериновый порох (кордит, балистит), способный гореть при высоких давлениях без детонации, в то время как оба исходных продукта чрезвычайно легко детонируют.
Второй способ образования рабочей смеси, именно смешение компонентов в камере сгорания, исключает возможность детонации при условии нормальной эксплоатации двигателя. Схема этого способа изображена на фиг. 58. Здесь каждый компонент топлива впрыскивается в камеру сгорания с помощью отдельной форсунки.
В данном случае смесь горит по мере ее образования, так что во время работы двигателя в нем отсутствует какое бы то ни было количество готовой смеси, не участвующей в горении, и тем самым устраняется опасность детонации.
Однако для того чтобы жидкая смесь сгорала по мере ее образования, необходимо иметь скорость сгорания все время больше скорости подачи топлива. В пределе при достаточно большом давлении в камере сгорания скорость сгорания может достигнуть скорости детонации. Это является идеальным случаем для рассматриваемого способа образования рабочей смеси, так как максимальной скорости сгорания отвечают минимальные размеры камеры сгорания и максимальный расход топлива при максимальном коэфициенте полноты сгорания, а следовательно, и максимальный к. п. д двигателя.
Особого внимания заслуживает комбинированный способ образования рабочей смеси, схемa которого показана на фиг. 59. При этом способе в камеру сгорания вводится через форсунку 1 смесь компонентов, взятая в такой пропорции, при которой она не обладает способностью детонировать. Недостающий для полного и правильного сгорания компонент вводится в камеру добавочно через форсунку 2. Благодаря этому облегчаются условия смесеобразования в камере сгорания, получается более совершенная рабочая смесь, и тем самым улучшается качество работы двигателя. Естественно, что этот способ непригоден в тех случаях, когда компоненты топлива при смешении вступают в химическую реакцию, или же когда топливные компоненты при одной и той же температуре находятся в различных состояниях. Например, предварительное смешение жидкого кислорода с каким-либо высококипящим углеводородом привело бы к затвердеванию углеводорода и нарушению правильности подачи топлива.
Смешение компонентов топлива может производиться в камере сгорания различными способами. Две жидкости могут смешиваться как в распыленном состоянии, так и в виде цельных струй без распыления.
Первый способ в настоящее время хорошо изучен и имеет широкое применение в двигателях Дизеля, в турбинах внутреннего сгорания, в двигателях с калильной головкой, в нефтяных топках и т. п.
В бескомпрессорных дизелях рабочая смесь получается путем впрыскивания жидкого горючего распылительной форсункой в камеру сгорания, наполненную сжатым газообразным воздухом, выполняющим функцию окислителя. Основная трудность состоит в получении достаточно быстрого и совершенного смешения распыленного горючего с газообразным воздухом, равномерно заполняющим камеру сгорания. На преодоление этой трудности было затрачено свыше 30 лет упорного труда и произведено множество интереснейших теоретических и опытных работ. Практического успеха в бескомпрессорном дизелестроении удалось достигнуть применением очень высокого давления впрыскивания (до 750 кг/см2).
Работа, затрачиваемая на впрыскивание горючего, составляет нормально 3–5% от мощности дизеля. Если учесть то, что в ракетном двигателе необходимо впрыскивать в камеру не только горючее, но и окислитель, которого по весу идет в 4–6 раз больше, чем горючего, то работа впрыскивания при столь большом давлении принимает весьма внушительные размеры. При этом и горючее и окислитель впрыскиваются в жидком виде, в связи с чем условия их смешения в сильной степени отличаются от тех, которые имеют место в бескомпрессорных дизелях.
Насколько оправдает себя способ образования рабочей смеси распылением, можно будет заключить лишь после ряда практических испытаний специально построенных ракетных двигателей.
Переходя к рассмотрению способа смешения компонентов топлива без распыления, отметим, что горение жидкой смеси может происходить и без предварительного ее испарения. Это весьма важное обстоятельство подтверждено рядом исследований (работы Альта, Вартенберга, Воллерса и Эмке, Засса и др). Более того, поскольку температура воспламенения горючего в жидком виде ниже температуры воспламенения его в газообразном состоянии, оказывается более выгодным получать и рабочую смесь в жидком виде. Это имеет большое значение, так как, при отсутствии необходимости в предварительном распиливании или испарении топлива, можно вести процесс смешения и сжигания в.весьма ограниченном объеме, т. е. иметь камеру малого веса.
Для смешения компонентов топлива в жидком виде без распыления были предложены различные устройства. На фиг. 60 показана схема двигателя, предложенная Г. Обертом. Камера сгорания имеет продолговатую форму и в донной части заканчивается конутом. Форсунки, подающие топливо цельной струей, расположены таким образом, что обе струи должны встретиться в вершине конуса. Вторая схема двигателя Г. Оберта, основанная на том же принципе, но с унитарной форсункой, показана на фиг. 61.
Эти две схемы нельзя признать удачными. В самом деле, трудно предположить, чтобы струя жидкости (в особенности низко кипящей, как азотный тетроксид, жидкий кислород и т. п.) диаметром в несколько миллиметров могла пронизывать пространство камеры,, наполненное вихреобразно движущимися массами продуктов сгорания, имеющих высокую плотность и раскаленных до 3000 — 4000°, и сохранять при этом жидкое состояние. Нет сомнения, что если не целиком, то в значительной мере струя будет испарена и раздроблена, а следовательно, смешение в жидком виде, предусматриваемое автором схемы, вряд ли будет иметь место.
|
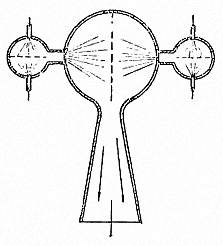
Фиг.63 |
|
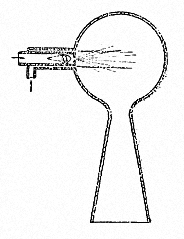
Фиг.64 |
|
Значительно более совершенной будет такая система смешения, при которой струи топливных компонентов встречаются непосредственно у входа в камеру сгорания, притом в ограниченном объеме и при непременном условии, что сжигание жидкой смеси происходит по мере ее образования. Схематическая конструкция двигателя, удовлетворяющая указанному процессу, представлена на фиг. 62. Отличительной особенностью этого двигателя является двухступенчатая камера сгорания. Первая ступень камеры, сообщающаяся с топливными баками и имеющая малый объем, служит для смешения компонентов и сжигания смеси в жидком виде. Вторая ступень, значительно большая по объему и непосредственно примы кающая к первой, служит для завершения процесса сгорания топлива в газообразном состоянии.
Таким образом первая камера является камерой предварительного сжигания, почему ее можно назвать форкамерой.
Преимущество этого способа образования рабочей смеси вытекает из того, что компоненты впускаются не отдельными струями в большую камеру сгорания, но смешиваются в незначительном объеме, занимаемом самим жидким топливом. Этим предупреждается раздробление струй и разброс компонентов, неизбежный при смешении в большом свободном объеме. Этот процесс существенно отличается от описанного способа предварительного смешения компонентов топлива (см. фиг. 57), так как в данном случае смесь горит по мере ее образования, и во время работы двигателя в нем отсутствует какое бы то ни было количество готовой смеси, не участвующей в горении. Другая схема форкамерного двигателя изображена на фиг. 63.
Помимо указанных основных систем смесеобразования возможен еще ряд комбинированных систем. На фиг. 64 изображена одна из таких систем, согласно которой один из компонентов топлива, проходя по центральному каналу унитарной форсунки, поступает в камеру сгорания в распыленном состоянии, в то время как другой компонент, проходя по внешнему каналу той же форсунки, впрыскивается в камеру сгорания в виде полого жидкостного цилиндра со сплошными стенками. Смешение компонентов происходит тотчас же после их выхода из ниппеля форсунки.
|
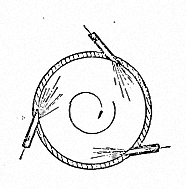
Фиг.65 |
|
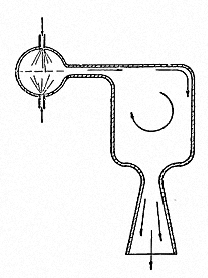
Фиг.66 |
|
Практика работы с двигателями внутреннего сгорания показывает, что полнота сгорания топлива и мощность двигателя значительно возрастают с появлением в камере сгорания интенсивного вихреобразования. Очевидно, что вихревые движения способствуют лучшему перемешиванию окислителя с горючим и образованию более однородной смеси.
|
Фиг.67 |
|
Заметные успехи были получены при сообщении рабочей смеси в камере сгорания организованного движения, также способствующего лучшему перемешиванию. С этой целью форсунки устанавливают в камере сгорания с некоторым скосом (фиг. 65), вследствие чего рабочая смесь приходит во вращательное движение. Тот же эффект достигается при соответствующем расположении канала, соединяющего форкамеру с большой камерой сгорания (фиг. 66). Для сообщения рабочей смеси определенного организованного движения в камере сгорания можно разбить камеру на ряд отделений с помощью перегородок, имеющих соответственно расположенные отверстия (фиг. 67). Для предупреждения расплавления эти перегородки должны охлаждаться.
Используя различные средства дня сообщения рабочей смеси беспорядочного или организованого вихревого движения, необходимо иметь в виду, что злоупотребление этими средствами может вызвать понижение к. п. д. двигателя. Эта область более, чем какая-либо другая деталь ракетного двигателя, нуждается во всестороннем экспериментальном исследовании.
Находясь в настоящее время в зачаточном состоянии, ракетный двигатель на жидком топливе все же не является таким беспомощным, какими были двигатели внутреннего сгорания в период их возникновения. Колоссальный опыт, накопленный в практике многолетней работы с тепловыми двигателями, создал ту базу, на основе которой ракетный двигатель имеет все шансы на быстрое и плодотворное развитие.
4. Поведение топлива в двигателе
Одним из важнейших моментов работы ракетного двигателя является воспламенение топлива при пуске и поддержание непрерывного равномерного горения.
Технические требования к воспламенению заключаются в безотказности зажигания в момент пуска двигателя как при любом запаздывании в подаче одного из компонентов топлива, так и при подаче в начальный момент любого количества топлива.
Свойства компонентов топлива могут оказать существенное влияние на работу механизма зажигания. Поэтому система зажигания непосредственно зависит от природы употребляемого топлива. При непрерывной подаче топлива в камеру сгорания достаточно получить лишь начальное зажигание в момент пуска. В дальнейшем горение будет поддерживаться от раскаленных стенок камеры и находящихся в ней продуктов сгорания.
В зависимости от назначения двигателя возможны два существенно различные способа их использования, требующие различных методов и механизмов для зажигания. Один случай – это однократный пуск, когда двигатель расходует при непрерывном горении весь имеющийся в аппарате запас топлива. Этот случай может встретиться, например в ракетных снарядах и торпедах. В другом случае могут потребоваться перерывы работы двигателя с несколькими повторными пусками и остановками без возможности подхода к двигателю между пусками. Примером может служить установка двигателя на самолете. В соответствии с этим мы будем различать однократное зажигание от зажигания повторного.
Понятно, что средства, пригодные для повторного зажигания, годятся и для однократного, но не наоборот. Как правило, механизмы повторного зажигания много сложнее, в связи с чем применение их для двигателя с однократным пуском нецелесообразно.
Органы зажигания, расположенные в камере сгорания, должны противостоять окислительной атмосфере и высокой температуре, развивающейся в камере, и давать достаточно энергичный и устойчивый воспламенительный очаг.
Зажигание при пуске двигателя должно действовать одновременно с началом пуска топлива в камеру сгорания и даже с некоторым упреждением, во избежание накапливания в камере жидкой смеси, что при запоздалом зажигании может вызвать разрушительный взрыв. После пуска двигателя зажигание должно поддерживаться до тех пор, пока двигатель не войдет в режим работы, хотя бы на минимальной мощности, т. е. пока не будет устранена возможность затухания, связанная с опасностью заливки камеры топливом.
Подавляющее большинство описанных в литературе взрывов ракетных аппаратов падает на момент пуска двигателя. В случае опоздания зажигания, по причине ли недостаточной его интенсивности или несвоевременности, в камере сгорания успевает накопиться некоторое количество топливной смеси, взрывающей или детонирующей в момент зажигания. Имея в виду, что жидкие топливные смеси являются сильнейшими бризантными веществами, нетрудно заключить, что надежность работы системы зажигания является важнейшим и необходимейшим условием нормальной и безопасной эксплоатации двигателя.
Вопрос о механизмах зажигания мало разработан в общей и патентной литературе, и решение этого вопроса, повидимому, потребует весьма обстоятельной и длительной опытной работы.
В своих опытах Г. Оберт производил зажигание топлива в ракетном двигателе с помощью зажженной тряпки, пропитанной бензином и намотанной на конец палки. Эта палка вводилась горящим концом в камеру сгорания через сопло. Несомненно, что такой прием не может быть рекомендован даже для лабораторных опытов ввиду его опасности. Оберт пользовался и другим приемом, именно вкладыванием в камеру сгорания пропитанной бензином тряпки, поджигаемой бикфордовым шнуром. Этот прием, хотя и более безопасный, чем предыдущий, все же неудобен.
Было предложено также производить зажигание после начала впуска топлива, поджигая струю топлива по выходе ее из сопла с помощью источника зажигания, расположенного на некотором расстоянии от сопла. Этот способ также небезопасен, так как может повлечь детонацию топлива.
Во многих предложениях встречается применение обычных электрических приборов для зажигания, именно искровой свечи и мостика сопротивления. Эти приспособления, отлично выполняющие свою роль в двигателях внутреннего сгорания и очень удобные в обращении, в ракетном двигателе пригодны только для некоторых сортов топлива и лишь для однократного пуска, так как они обычно расплавляются, сгорают и дают неустойчивый, незначительный по размерам очаг, который легко может быть залит струей топлива. Более надежным является зажигание с помощью медленно горящего порохового заряда, помещаемого в камере сгорания и в свою очередь воспламеняемого от электрической цепи, как это предусмотрено уже упоминавшимся французским патентом № 502562. Понятно, что для повторного пуска этим же же приемом пришлось бы вновь ввести пороховой заряд в камеру сгорания, для чего потребовалось бы создание специального магазина с автоматическим устройством для подачи пороховых зарядов в камеру.
Наиболее удобным средством как для однократного, так и для повторного зажигания следует признать химическое зажигание с помощью впрыскиваемой в камеру активной жидкости, способной воспламеняться при соприкосновении с одним из компонентов топлива. Такие жидкости известны (например, раствор фосфора в сероуглероде), и применение их неоднократно предлагалось также и для двигателей внутреннего сгорания.
Обратимся теперь к рассмотрению способов защиты частей двигателя от разрушающего влияния высокой температуры.
Этот вопрос также представляет немалые трудности, обусловливаемые тем, что температура в камере сгорания доходит до 3500°. При этой температуре все известные и технически доступные материалы плавятся, а в большинстве случаев даже кипят.
В особенно тяжелых условиях находится сопло, в частности его критическое, сечение, подвергающееся одновременно и сильному нагреву и трению со стороны газового потока, истекающего под большим напором.
Выгоранию частей двигателя способствует еще то, что окислитель обычно является химически сильно деятельным веществом.
Задача предохранения ракетного двигателя от разрушения несколько облегчается тем, что в отличие от обычных двигателей внутреннего сгорания работа его, как правило, кратковременна, а в некоторых случаях, как, например, при применении в снарядах, ограничивается лишь однократным действием.
В обычных двигателях для понижения температуры в камере сгорания прибегают к увеличенному впуску воздуха (так называемое обеднение смеси), а также к впрыскиванию воды. Оба эти приема непригодны для ракетного двигателя: первый потому, что необходимый для горения запас этого окислителя помещен в самом аппарате и расходование его не по прямому назначению снизило бы радиус действия аппарата; второй – потому, что введение инертной примеси привело бы к снижению мощности двигателя, не говоря уже о том, что запас воды в аппарате должен пойти за счет полезного груза.
По этой же причине для ракетного двигателя нецелесообразно применять обычное проточное водяное охлаждение наружных стенок, тем более что оно связано со значительными тепловыми потерями. Последние, например в двигателях внутреннего сгорания, достигают 30% от всего количества развивающегося в цилиндре тепла.
Из сказанного ясно, что борьба с выгоранием в ракетном двигателе представляет известные особенности и не может быть решена теми же путями, какие применяются в обычных двигателях.
Один из возможных путей заключается в том, чтобы отводить тепло от наиболее нагреваемых частей двигателя. Этого можно достигнуть применением материалов с высокой теплопроводностью. Наиболее подходящим материалом является красная медь, которая лучше сопротивляется разгару, чем сталь, несмотря на то, что ее температура плавления на 300–400° ниже, чем стали. Из практики известно, что автогенная сварка красной меди возможна лишь в тонких листах, так как из-за высокой теплопроводности металл с трудом нагревается до нужной температуры. В то же время сварка железных листов не представляет никаких затруднений при любой толщине.
Оберт и другие исследователи успешно применяли красную медь в качестве материала для камеры сгорания при работе с таким высококалорийным топливом, как смесь жидкого кислорода с углеводородами. Из других металлов заслуживает внимания хром, который наряду с химической стойкостью и высокой теплопроводностью обладает также и высокой температурой плавления (1700°). Такие металлы, как алюминий и магний, хотя и обладают хорошей теплопроводностью, непригодны для рассматриваемой цели, так Как имеют низкую температуру плавления (около 650°).
Применение хорошо проводящих тепло металлов выгодно сочетать с наружным проточным охлаждением нагреваемых частей, используя для этого компоненты топлива. Такой способ, помимо устранения излишнего груза в виде воды, может дать существенное улучшение работы двигателя. Во-первых, теплота, отданная стенками топливу, не пропадает целиком, но сохраняется в тепловом балансе двигателя, так как топливо, поступая в камеру сгорания подогретым, требует меньшей затраты тепла для нагревания его до температуры воспламенения. Во-вторых, подогрев топлива уменьшает его вязкость и поверхностное натяжение, а следовательно, облегчает распыление и смешение компонентов в камере.
Однако следует иметь в виду, что топливо до поступления в камеру не должно превращаться в газообразное состояние, иначе будет нарушен правильный режим горения в камере. Поэтому для целей охлаждения следует использовать тот из компонентов топлива, который обладает высокой температурой кипения. С этой точки зрения использование сжиженных газов (например жидкого кислорода) для охлаждения не может быть признано целесообразным.
На фиг. 68 показана схема двигателя с проточным охлаждением. Здесь один из компонентов топлива подается непосредственно из бака в камеру сгорания, второй же компонент предварительно проходит через полость между камерой и рубашкой и после этого попадает в форсунку.
Второй способ борьбы с разгаром двигателя состоит в защите нагреваемых частей теплоизолирующим покровом, способным противостоять высокой температуре, развивающейся в камере сгорания. В технике известен целый ряд материалов, обладающих очень высокой температурой плавления. По химическому составу они могут быть разделены на две главные группы. К первой относятся так называемые карбиды, т. е. сплавы углерода с металлами или металлоидами, во вторую же группу входят окислы некоторых металлов.
|
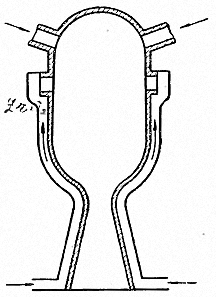
Фиг.68 |
|
Некоторые карбиды обладают чрезвычайно высокой температурой плавления. Например, тантал-карбид и ниобий-карбид плавятся при 4100°. Чистый уголь и графит имеют температуру плавления 3600–3700°. Однако для ракетного двигателя защитные покровы из карбидов или углерода непригодны, вследствие того что в камере сгорания всегда может оказаться избыточный окислитель, а это повлечет за собой выгорание содержащегося в карбиде углерода и разрушение изолирующего покрова. Опыты Оберта с графитовыми, карборундовыми и т. п. покровами целиком подтверждают это положение.
Значительно более благоприятные результаты должно дать применение тугоплавких окислов металлов. Среди них первое место занимает окись циркония O2 с температурой плавления 2950°, затем окись магния MgO, плавящаяся при 2800°.
Создание прочного теплоизолирующего слоя, однородного по строению, с небольшой толщиной для избежания чрезмерного веса, с достаточно гладкой поверхностью для возможного уменьшения разрушающего влияния трения газов, представляет собой достаточно сложный комплекс задач, для решения которых потребуется обширная исследовательская и опытная работа.
В заключение этой главы остановимся еще на вопросе о выборе материалов для деталей двигателя.
Для тех частей, которые подвергаются сильному нагреванию, следует применять огнестойкие материалы. Помимо электролитической меди, о которой мы уже упоминали, широкое применение должны найти жаростойкие стали типа «Энерж 7» завода «Электросталь».
Для топливных баков, для рубашек наружного охлаждения и для трубопроводов целесообразно применение алюминиевых и магниевых сплавов, которые хорошо сопротивляются разрушающему действию кислот, а при действии низких температур (жидкий кислород) не теряют своих механических качеств.
Для тех деталей, которые должны обладать химической стойкостью, например в случае применения азотной кислоты, азотного тетроксида и т. п., наилучшим материалом является нержавеющая сталь типа «Энерж 6» завода «Электросталь» или марки V2A завода Круппа. Алюминий и его сплавы также могут применяться с успехом для той же дели, но только для тех деталей, которые не подвергаются действию высокой температуры. Наконец, при необходимости применить тот или иной материал, способный подвергаться коррозии, его можно покрыть защитным слоем некорродирующего материала, например хромированием, золочением и т. п.
Подводя итог сказанному в этой главе, мы еще раз подчеркиваем, что задача создания мощного, надежно работающего ракетного двигателя представляет собой целый ряд новых технических проблем, большинство которых находится в совершенно зачаточном состоянии. Для конструктора, экспериментатора и изобретателя здесь непочатый край работы. Успешное решение задачи может быть лишь плодом их коллективного труда.
* * *
|